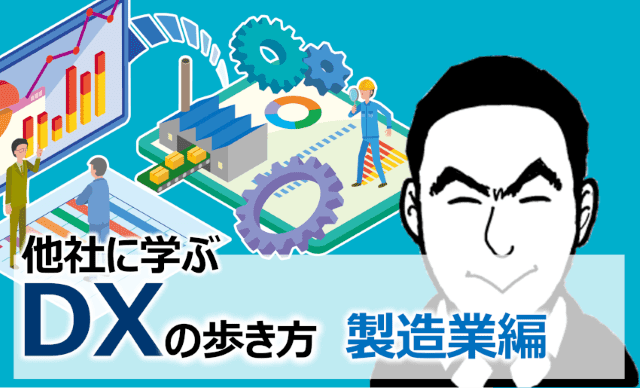
業務・経営データ収集の迅速化による真のデータ経営の実現(他社に学ぶ DXの歩き方コラム 製造業編第1回)
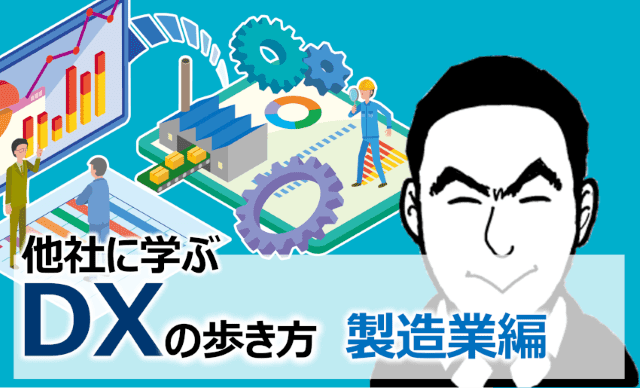
目次
はじめに
多くの中堅中小製造業では、営業部門、生産管理部門、製造部門ともにバラバラなデータ管理を行っている事が経営課題になっています。
例えば営業部門では、各営業担当者が自身のパソコンに保管してある過去の見積書を使用し、数年前に設定した標準原価から営業担当者の判断で利益を上乗せしてお客様へ提示をしており、生産管理部門では、特定のスタッフがExcelを使って生産計画書を作成し、頻繁に発生する特急注文による山積み山崩し等が発生すると、その修正が後回しになり、Excelの修正にも多大な時間を要している状況が見受けられます。
一方で製造部門では、実際の出来高を手書き日報等に記入はしているものの正確にデータ化できていない状況にあります。
また、原材料の発注に関しては、製造部門スタッフが部材置き場に置いてある部材が減ってきた状況を見て、台帳等に発注希望個数を記入し、購買担当がそれを1日2回見て、必要な部材を業者に発注している状況になっており、現場の裁量で発注されていることで材料が過剰な在庫状態になっていることが課題となっています。
経営者としては、生産に掛かっている実際の時間を把握して、製品毎の標準原価を設定し、システム上で製品在庫および、原材料在庫を把握して棚卸回数を減らすだけでなく、適正在庫を維持する事で材料コストだけでなく人件費も低減したいと考えています。
また、製品別や得意先別に実際どれくらいの利益が出ているのか、製品を出荷するまでの工程において、現状どれくらいの工数および金額が掛かっているのか、見える化を実現することで、適正な利益を上乗せした見積を提示する事が可能となり、生産の現場の改善にもつなげたいと考えています。
このような現状の中、「データ経営」で効果を出している企業は、どのようなアプローチで、どのような仕組みを作って運用しているのでしょうか。
金属機械加工製造業B社の事例をご紹介します。
B社 DX事例
B社では、20年前に生産管理システムを導入して運用をしていましたが、販売と購買の機能が不足しており、Access等を駆使して業務を回しておりました。
しかし、至る所で二重三重業務が発生しており、製品在庫や原材料在庫がシステムで把握できない事も大きな課題になっていました。
そこで、社長が業務改革を踏まえたシステム刷新を行う事を決断し、下記のプロセスで進める事で、システム導入当初は生産性が下がったものの、稼働6か月で旧業務運用時に比べ10%以上生産性が向上し、成功に導く事ができました。
成功の要因は下記の6点であると考えられます。
- 現状業務で属人化されている業務および二重三重で行っているボトルネック業務の洗出しを行った。
- 社長自ら経営判断に必要な指標を明確化し、メンバーに共有した。
- 業務改革の範囲を明確にした上で、これに適した統合型の生産管理・販売管理システムを導入し、このシステムの導入に合わせて業務標準化を進めた。
- 上記の導入のタイミングで運用上のルールを改定し、標準化を進めた。
- 基幹システムのデータを基に分析ツールで経営判断に必要なデータを可視化できる仕組みを構築した。
- システム稼働後も自社でデータ収集およびデータ分析できる為のトレーニングを2月実施し、概ね自分達で運用可能となった。
また、B社では、社長が見たいデータをBIツールを使って実現化しました。経営データ分析を行う為に、受注~購買~入荷~生産計画~製造実績~在庫~出荷等のデータをBI上に格納し、これを多角的に抽出、加工する事で経営判断に必要なデータを容易に可視化する事ができました。
まさにこの事例は、基幹システムと連携するBIツールが「真のデータ経営の実現」ではないでしょうか。
今回導入・活用したサービス
- BI:Microsoft Power BI(Microsoft Dynamics 365)
「DX推進」に関しましてはディーアイエスサービス&ソリューションまでお気軽にお問い合わせください。
本コラムは2021年11月現在の情報を基に作成しています。