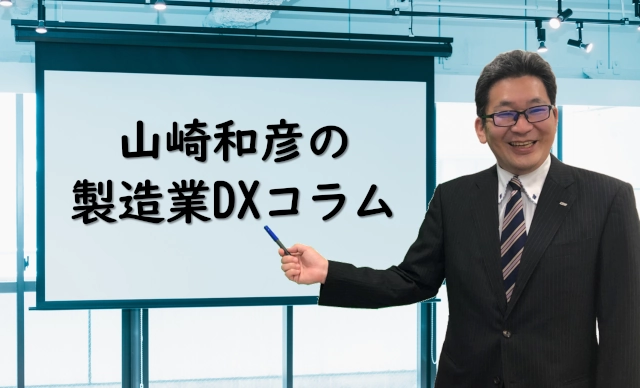
「IoT、AIを活用した生産管理によって、製造ロスの大幅削減を実現した成功事例」山崎和彦の製造業DXコラム 第5回
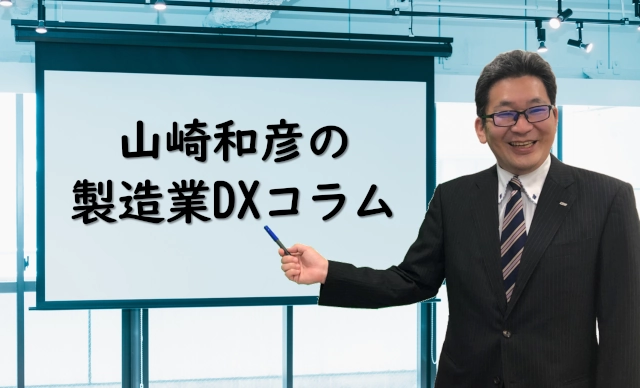
はじめに
総務省「令和元年版 情報通信白書のIoT・AIの導入状況と今後の意向(※1)」によると、日本は、中国・米国・欧州主要4か国の中でAIに積極的な取り組みをしている企業が39%と最下位です。
また産業別で比較するとテクノロジー/メディア/通信業界では比較的差が少ないものの、その他の産業では大きく後れを取っています。今回はその他の産業におけるIoT、AIを活用して成功を収めた事例をご紹介します。
※1:総務省令和元年版 情報通信白書 第1部 特集 進化するデジタル経済とその先にあるSociety 5.0
https://www.soumu.go.jp/johotsusintokei/whitepaper/ja/r01/html/nd112220.html
業務改善に取り組む背景と目的
U社は、蒲鉾やちくわなどの練り物の製造、販売を行っている老舗の食品業で、従業員数約300名、売上高が約85億円の企業です。
AI、IoTを活用した製造部門の効率化を通して利益率向上を実現するプロジェクトを発足し、各製造部門のヒアリング・調査を行ったところ、以下のような課題と要望を抽出できました。
- 生産工程の自動化は進んでいるが、成型・加熱工程を経た後に規格外品が多く発生している。また、発生原因が掴めていない。
- 成分、風味、サイズなどが多様な為、その規格外品の再利用を行うのが難しい。そのため、多くは廃棄ロスに繋がっている。
- 検査工程は主に目視で行われていて、焼き目などの見た目が判断基準となる為職人の肌感覚に頼らざるを得ない。
- 規格外品の発生には連続性があるものの、生産工程の稼働状況が正常なのかどうかを判断する材料が無いため、事前に製造ロスを防げないでいる。
製造ロスに関しては以前から課題として現場では認識されていたものの、解決が難しいとされてきました。 U社ではちくわがメイン商材であったため、業務インパクトが大きい課題であると判断し、まずはこの部分を改善ターゲットとすることを決定しました。
ちくわの製造は以下4つの工程で行われます。
- すり身を各種調味料と混ぜ合わせる擂潰(らいかい)という工程
- シート状にしたすり身をステンレス製の棒に巻き付ける成型工程
- 中心温度90度になるように設定した機械を通して蒸し焼きにした後、直火で焼き目を付ける焼き工程
- .棒から外して急速冷却後に検査する検査工程
その中でも2.成型工程と3.焼き工程で規格外品が多く出てしまう状況が続いていました。
業務改善の目標
業務改善にあたり、まずは以下を目標として設定しました。
- 製造ロス発生数の減少(50%)
業務改善への取り組み
業務改善にあたり、まず、以下の内容を含む企画・計画を策定しました。
- 推進範囲と段階的な導入シナリオ
- 目的、目標達成に向けた改善策
- システムツール導入を含めた改善スケジュール
取り組みのポイントは以下の通りです。
①製造ロスの原因と想定される範囲の設定
過去の実績データを分析すると、製造ロスの原因は焼き色に関するもので50%近く、成型不良が30%近くを占めていることが分かりました。成型不良の原因としては大きさや形が規程閾値から外れている、焼き色に関しては濃い、薄いなどが挙げられます。また、成型不良によって厚みが異なる場合は焼き色不良を伴うケースが多い一方で、焼き色不良に関しては成型が規定値内でも起こっていることが分かりました。このことから、焼き工程を中心とした成型~焼き工程までの各データを抽出することとしました。
②成型工程のデータ収集の実施
成型工程では巻き付けられたすり身の厚み、長さの計測を行うカメラを設置しました。測定の結果、規定値を超える、あるいは下回る成型は連続して現れることが分かりました。さらなる分析の結果、擂潰工程後にすり身をシート状に整える作業部分で、連続作業時間が一定時間を超えると詰まりが発生しやすくなり、結果成型に不良が出やすくなっているということが分かりました。
③温度計測センサーを用いたデータ収集の実施とAI活用
次に、焼き工程に温度計測センサーをはじめとした各種センサーを設置しました。各工程の直前・直後の表面温度データを計測するものです。このデータに加えて、直火での温度設定と通過時間、製造ロス発生数を抽出しました。様々な設定でデータの抽出を繰り返し、AI技術を用いて分析することで、もっとも製造ロスを抑えられる各製造工程の表面温度規定閾値の設定見直しを行いました。
業務改善による効果
上記のような取り組みを経て、以下のような効果が得られ、目標を達成しました。
- 製造ロス発生数の削減(約80%減)
月間で300kgほどの製造ロスが起こっていたU社では、今回の取り組みを経て製造ロスを大きく削減することに成功しました。170gで1梱包とした場合、月間1800食近く発生していた製造ロスは、月間350食程度まで削減できました。焼き色は安定し、成型不良も事前に食い止めることができたことが大きな要因といえます。
- 工程トラブルの事前察知、対策の仕組み化
本ケースにおいては、連続稼働時間と焼き工程に入る直前の表面温度がポイントとなりました。
成型工程の不良対策として、擂潰工程後にすり身をシート状に整える作業部分での連続作業時間が一定時間経過後に必ず一部部品の清掃を行うようにしたことで成型不良を防ぐことができるようになりました。また、焼き工程不良に関しては、各工程の直前、直後の表面温度が規定閾値を逸脱した場合アラートを出して確認作業を行うようにしました。
- 現場製造状況の可視化と、AIの活用拡大
センサーなどを用いた現場の可視化により、職人の肌感覚が強かった安定製造のポイントを、データを用いて議論が出来るようになりました。また、焼き工程の温度設定・投入時間と不良品に関するデータを蓄積したことで、状況に応じてベストな加工設定を判断することもできるようになりました。
今回導入・活用したサービス
- 温度計測センサー、カメラ(IoT)
- AI
「DX推進」につきましては、ディーアイエスサービス&ソリューションまでお気軽にお問い合わせください。
本コラムは2023年3月現在の情報を基に作成しています。
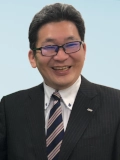
著者プロフィール
山崎 和彦
兵庫県出身。1998年入社、大手産業機械メーカの生産管理システムを含め多様な業種・規模のシステムを導入・支援を実施。入社以来、生産管理のみならず会計・販売管理の提案・販売に従事。基幹系、生産管理系両方の視点を持っていることにより近年、顧客のDX推進に軸足をおき提案活動を行っている。工場設備の稼働状況を可視化するモニタリングシステムの導入や、製造情報・検査情報のトレーサビリティ強化など現場での各情報をデータベース化することでお客様の品質・コスト・納期の諸問題を解決し業務効率化に貢献している。