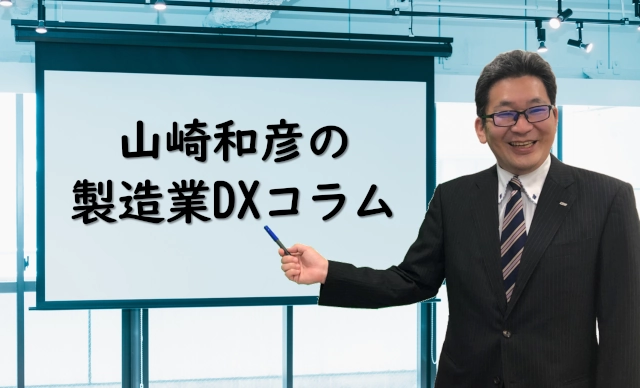
「リアルタイムでの在庫管理による、効率的な材料の調達実現事例」山崎和彦の製造業DXコラム 第2回
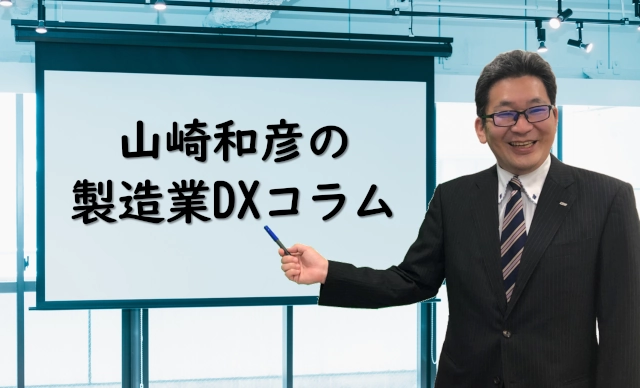
はじめに
昨今、日本の製造業を取り巻く環境は非常に困難なものとなっています。
新型コロナウイルスの影響により、日本の2020年4~6月のGDP成長率は年率比約29%ダウン(※)と1995年以降過去最大の落ち込みであったと報告されています。さらにウクライナ情勢の悪化などを背景に、円安、原油高が進み、原材料価格の高騰も起きています。
多くの資材、原材料を輸入に頼る日本にとって、この状況下においては商品の値上げは避けられない状況になりつつあり、様々な面でのコスト削減や、省人化、業務効率化を通していかに競争力を確保するかという点が大きな関心事項であるといえます。
今回は、DX推進の一環としてリアルタイムな在庫管理の実現による材料調達の最適化に取り組み、経営状況を大きく改善した事例をご紹介します。
※経済産業省「2020 年版ものづくり白書」より
https://www.meti.go.jp/report/whitepaper/mono/2021/pdf/honbun_1_1_1.pdf
DX推進に取り組む背景と目的
食料品の添加物・副材料メーカーのP社では、取引先からの要望に合わせてレシピ開発を行い、食料品製造に使用する添加物や副材料の生産・販売を行っています。
コロナ禍の影響から受注量が減少し経営状況が悪化したことから、より無駄の少ない効率的な生産を実現できないかと社内体制の見直しを図ることとなりました。
そして、社内状況の調査、分析を行い以下のような問題が明らかになりました。
- 原材料の発注業務が属人化しており、過剰な仕入れによる原材料の廃棄ロスが発生していた
- 見込み生産分の一部が廃棄処分となっていた
- 出荷する副材料を利用した製品の製造情報(増産、減産、製造中止など)が担当部署に共有されておらず、製造スケジュール、数が出荷ギリギリまで不明となっていた
特に問題となったのは、勘や経験に基づく需要予測とそれに紐づいた発注業務・在庫管理にありました。
食料品に利用されるということもあり、消費期限などの関係で事前に材料を多く仕入れすぎても廃棄に繋がり、少なすぎれば生産が間に合わなくなります。
見込み生産分に関しても、食品の場合は早く作りすぎてしまえば消費期限の問題で廃棄に繋がってしまいます。
このような原材料、見込み生産分の廃棄ロスは利益率に大きな影響を与えます。高い精度の在庫管理と材料調達を行うには需要に関する十分な情報が必要ですが、それに関してしっかりと情報共有できているとはいいがたい状態であることが明らかになりました。
そこでP社では “適正在庫管理を通した調達の最適化“をキーワードにDX化を目指すこととなりました。
DX推進への取り組み
DX推進にあたり、まず、以下の内容を含む企画・計画を策定しました。
- 在庫管理におけるDX推進範囲と段階的な導入シナリオ
- 目的、目標達成に向けた改善策
- システムツール導入含めた改善スケジュール
上記のような企画・計画を策定した上で、DX推進によるリアルタイムでの在庫管理の実現に取り組みました。取り組みのポイントは以下の通りです。
①従来の手法の確認と適正在庫の定義
適正な調達を行う為には、現時点での在庫量が適正であるかどうかの判断を行う基準が必要です。
適正在庫基準の定義にあたって重要となるのは、実際の受注に必要な原材料に加えてどれくらいの余剰材料、製品在庫(下記、安全在庫と適正在庫の関係を参照)を持つべきか、という点です。
この点は、現場の人間の勘と経験によって判断されており、このブラックボックスな部分をヒアリングしながら解き明かすことから始めました。
結果、過去の生産実績、季節情報、月々の平均的な在庫利用量や、商談中の案件情報、生産現場の仕掛状況などから判断していたことが分かりました。
安全在庫と適正在庫の関係
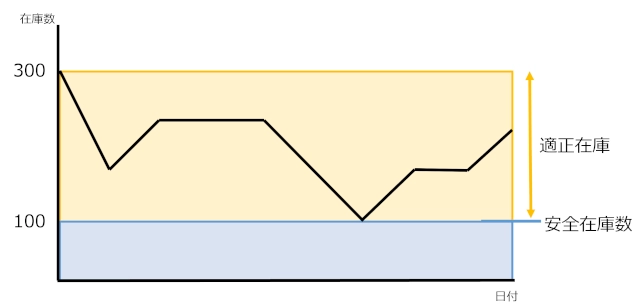
安全在庫:欠品を防ぐための在庫下限値のこと
適正在庫:欠品せず、過剰在庫にならない在庫数のこと
※安全在庫の算出には、一定期間での使用量の標準偏差や、平均的な発注リードタイム、発注間隔などが必要です。
※適正在庫の算出には、一定期間に必要となる需要数が必要です。
②必要なデータの抽出
次に、適正在庫を定義するのに必要な過去データを抽出することとしました。
まず、過去7年分の受注データ、原材料の発注データ、仕掛品データ、在庫量推移データ、廃棄ロスデータなどの抽出を行いました。
次に、生産進捗の把握を通して、現在どれくらいの個数が生産完了しており、製造途中に発生した不具合件数(製造ロス)はどれくらい生じており、結果として現在の在庫状況はどのような状況であるのか、を把握するための仕組みづくりを行いました。
こちらは、製造工程別に実績情報を抽出する必要があるため、各工程でタブレットを利用して生産状況を閲覧する方法を取り入れました。
この仕組みでは、指図書に基づく原料の投入タイミング、天候状況、温湿度やミキサーでの撹拌回転数等のデータを生産管理システムと製造機械から取得し、リアルタイムに工程ごとの生産状況と出来上がり予測や工程間在庫や完成品在庫状況を把握することができるようになりました。
③機械学習式AIを用いた適正在庫量、調達業務の仕組み化
安全在庫の設定と、適正在庫量の決定を行うには、確定している数字だけではなく、飛び込みで入る受注情報などの不確定な情報を考慮する必要があります。こういった需要情報は日々変化するため、適正在庫量は都度変化していきます。
これまでは過去のデータを参考に経験豊富な従業員がこの需要予測を行っていましたが、実施する頻度が高く、時間もかかり、判断基準も担当者の勘に近い状況だったこともあり、この判断に関しては機械学習式AIを活用することとしました。
先に述べた取り組みシステムとあらゆるデータをAIに読み込ませ、そのデータを利用した生産シミュレーションシステムを構築しました。
このようにして安全在庫、適正在庫の目安となる数値と、それに伴う適正な発注量目安を把握することができるようになりました。
DX推進による効果
上記のような取り組みを経て、以下のような効果が得られ、目標を達成しました。
- 廃棄ロス(原材料・製品)の削減(30%削減)
AIを用いた適正在庫量の判断が行われ、それに基づいた仕入れ・調達を実施しました。過剰な仕入れ、それに伴う廃棄ロスは大きく削減することができました。初期は精度があまり高くなかったため予想を超えた注文が入った際の機会ロスを心配していましたが、内示情報などもリアルタイムで更新されるので必要在庫量が大きく乖離することは少なく、修正にも時間を要しませんでした。
- リアルタイムでの在庫管理の実現と、より良い生産計画の実現
様々な生産工程データを抽出することはリアルタイムでの在庫管理だけでなく、生産計画との乖離を確認する上でも必要な内容でした。これにより、生産計画もより実情に沿った形のものとなり、結果、適正在庫量の判別精度が向上しました。
- 在庫管理業務属人化の解消
以前は担当者が勘と経験を頼りに発注を行っていましたが、購入すべき目安が自動算出される仕組みとなったため担当者に求められるのは発注する数値の確認と実際の発注判断だけになり、在庫確認から調達にかかる業務を大幅に効率化することができました。また、在庫調査・棚卸なども在庫数を数値で管理できているため、簡単に行うことができるようになりました。
今回導入・活用したサービス
- 生産シミュレーションAIシステム(オリジナル構築)
- 生産モニタリングシステム
「DX推進」につきましては、ディーアイエスサービス&ソリューションまでお気軽にお問い合わせください。
本コラムは2022年7月現在の情報を基に作成しています。
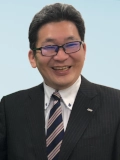
著者プロフィール
山崎 和彦
兵庫県出身。1998年入社、大手産業機械メーカの生産管理システムを含め多様な業種・規模のシステムを導入・支援を実施。入社以来、生産管理のみならず会計・販売管理の提案・販売に従事。基幹系、生産管理系両方の視点を持っていることにより近年、顧客のDX推進に軸足をおき提案活動を行っている。工場設備の稼働状況を可視化するモニタリングシステムの導入や、製造情報・検査情報のトレーサビリティ強化など現場での各情報をデータベース化することでお客様の品質・コスト・納期の諸問題を解決し業務効率化に貢献している。